Table Of Content
- the passenger experience
- Gensler releases plans for winged Flight Test Museum in California
- Design process and simulation
- This Bonkers New X-Plane Uses Holes in Its Wings to Hit Mach Speeds
- Future US Military Rotorcraft Design Capability At Risk
- Products & Services
- Foster + Partners designs sweeping terminal for "air taxi services" in Dubai
The jet engines also can power generators to directly supply electricity to the electric motors, or to charge batteries for the electric motors to use later. This can mean an all-electric airplane in which electric motors turn propellers or fan blades to generate thrust. Such a capability could enable all sorts of new ways airplanes could be designed, either by modifying current airplanes or coming up with new configurations. It must move through the air easier, possibly use electricity to augment or power the propulsion system, and it must be as lightweight as is safely practical.
the passenger experience
My work specifically has related to calculating the aerodynamics of the propellers and modeling how prop-wash can affect the aerodynamics of lifting surfaces, like wings. Using this tool, aspiring aircraft designers with little to no knowledge of aerodynamics or aeronautical engineering can design their own aircraft. From a simple flying wing to a canard with distributed electronic propulsion, MachUp allows users to design their own aircraft and easily analyze its aerodynamics. During the design phase, the definition and dimensioning of all elementary parts and their interfaces are performed, and the equipment, engines and landing gear are developed by the supply chain. In the integration and qualification phases, parts are produced and assembled – both for test specimens on test benches and for the first aircraft that will serve the flight test programme. The tests are organised as a pyramid, going from lab tests at a small scale (via integration tests for checking the behaviour of complete systems) to full-scale structural tests and flight tests.
Gensler releases plans for winged Flight Test Museum in California
Five other Airbus design offices and engineering centres are located throughout Europe, with sites in Germany, Spain, the UK, and Russia. Each bring their specific competencies in areas such as fuselage structures, landing gear, fuel systems, composites, tooling, cabin interiors and cargo compartments. The engineering of a new aircraft today is deeply immersed in the digital world.
Design process and simulation
Soon those cases could influence propulsion, engine integration and wing technology choices that will determine the blueprints for a new generation of fuel-efficient aircraft. Like the commercial competition in the 1990s, today’s vertical flight engineers are a hot commodity for the booming electric VTOL aircraft industry. With commercial salaries and benefits much higher and bureaucratic red tape much lower, these companies are hiring top talent to develop and bring their VTOL aircraft to market. Dassault also applied lessons learned from the carbon-fiber wing on its Rafale fighter to its Falcon 10X business jet, which is prepping for flight tests. According to Carlos Brana, Dassault’s executive vice president of civil aircraft, using the carbon-fiber technology saved the company from “starting from scratch” on a new wing design.
This Bonkers New X-Plane Uses Holes in Its Wings to Hit Mach Speeds
The new limited-edition cards are cloud-white in color and made from two Delta Boeing 747 aircraft1 that were retired after more than 27 years of service and feature each plane’s history, including their first and last flights, tail number and number of miles flown. Sikorsky — teamed with Boeing — lost the FLRAA competition and laid off hundreds of engineers last year. Alexander says this platform is largely the same as the design the company submitted for CCA. It shares the same landing gear and primary structure with a slight change to the wing slope.
In order to succeed, it is important to properly frame your issue by identifying key design requirements. Creating a process map is the first step towards designing and building a new aircraft. Aviation’s decarbonisation relies on a mixture of incremental steps and outright technological breakthroughs. In this spirit Airbus, DLR and ONERA, two leading European research institutions, are exploring how high-performance computing can improve our understanding of the relationship between aerodynamics and aircraft efficiency.
Could DARPA's enigmatic X-65 plane revolutionise aircraft design? - New Scientist
Could DARPA's enigmatic X-65 plane revolutionise aircraft design?.
Posted: Thu, 18 Jan 2024 08:00:00 GMT [source]
Products & Services
In previous articles we discussed how to avoid major mistakes as a mechanical engineer, these design processes are excellent examples of how you can help to avoid errors. Similar to, but more exacting than, the usual engineering design process, the technique is highly iterative, involving high-level configuration tradeoffs, a mixture of analysis and testing and the detailed examination of the adequacy of every part of the structure. For some types of aircraft, the design process is regulated by civil airworthiness authorities.
“We decided that unified controls is a proven direction to go,” he says, referring to systems that allow vertical takeoffs and landings to be executed with one hand. The advanced systems relay commands every few milliseconds via pilot input to help automate flight, the endgame being a much safer, more intuitive generation of aircraft. MachUp is a free, online aerodynamic analysis tool used for aircraft design, analysis, and optimization. This tool was developed by graduate students under the leadership of Dr. Doug Hunsaker at Utah State University. I myself have been working on the development of MachUp for over a year now.
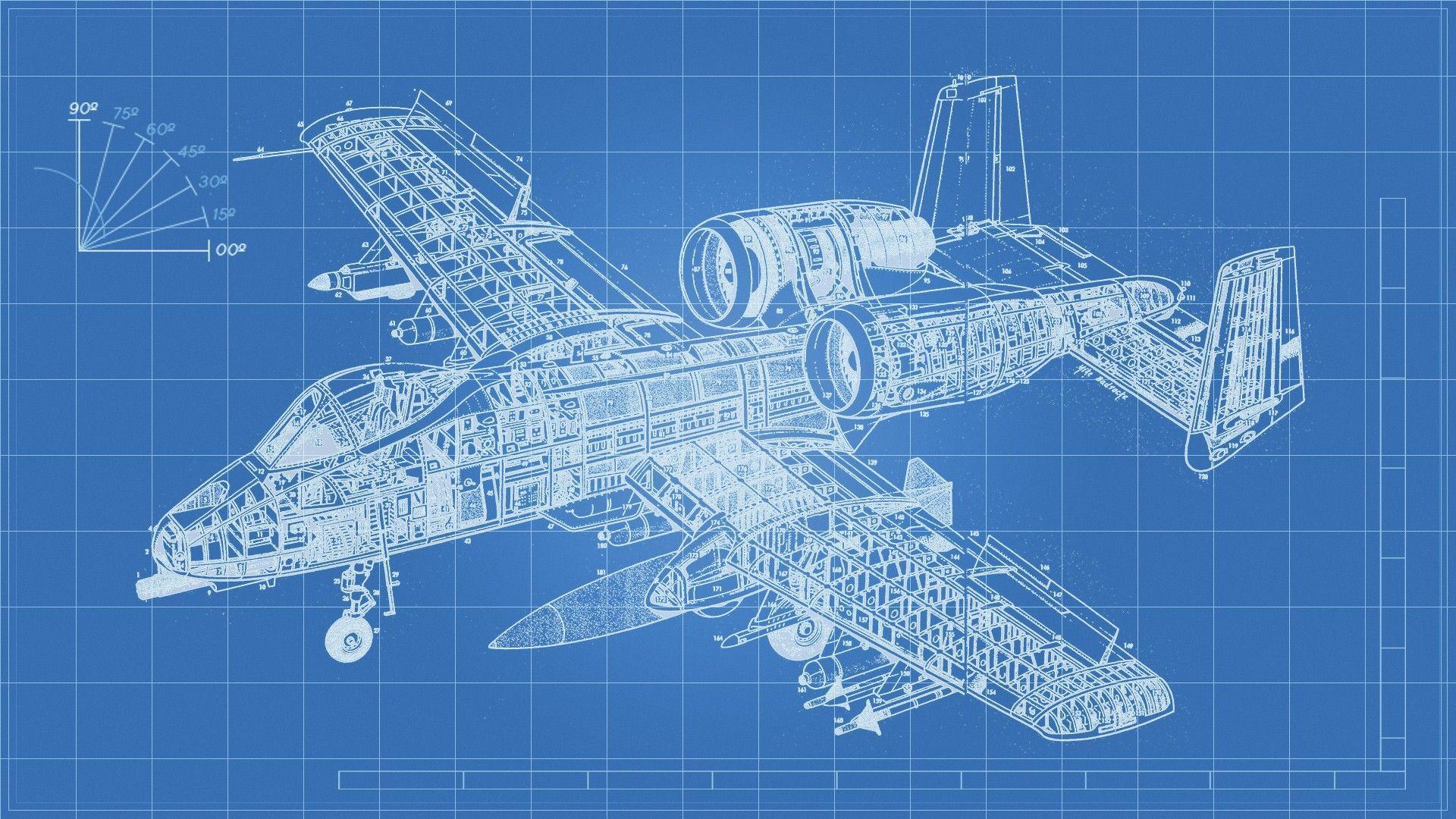

Boeing similarly has decades of production and support contracts remaining for its CH-47 Chinook, AH-64 Apache and other military rotorcraft. Army Signal Corps bought a Wright Military Flyer from the Wright brothers for $30,000, and has kept apace for more than a century as dozens of aircraft types were converted for the armed forces. Military-technology transfer is now advancing even more rapidly into the civilian market, with the latest generation of electric aircraft currently undergoing flight testing in preparation for certification in the next few years. At first glance, private jets and military aircraft couldn’t seem further apart. But in the gray area between coddling luxury and mission-based efficiency, there’s a rich history of innovation exchange that has helped both categories stay on the bleeding edge of aviation.
The final product is a conceptual layout of the aircraft configuration on paper or computer screen, to be reviewed by engineers and other designers. The design configuration arrived at in the conceptual design phase is then tweaked and remodeled to fit into the design parameters. In this phase, wind tunnel testing and computational fluid dynamic calculations of the flow field around the aircraft are done. Aerodynamic flaws and structural instabilities if any are corrected and the final design is drawn and finalized. The white space tackled by eVTOLs has brought with it the opportunity to invent new flight-control systems for easier, safer operation. “We’d been researching the best way to control a vehicle of this class,” explains Joby Aviation’s Peter Wilson.
“We can invest in the things that are for the greater good, but we don’t build, produce, or operate commercial airplanes. We just develop technologies so that industry can competitively bring these to market as desired,” Kenyon said. They can be fabricated into complex shapes, are structurally stronger and weigh much less than the same parts made from metal. The problem is the nacelle of an engine hanging off the wing of an airliner can only be so big in diameter before it starts dragging on the ground.
Galpin oversees a five-year-old partnership with French aerospace lab ONERA (Office National d'Etudes et de Recherches Aérospatiales) and the German Aerospace Center DLR (Deutsches Zentrum für Luft- und Raumfahrt) on behalf of Airbus. The answer is that all these efforts are part of NASA Aeronautics’ Strategic Implementation Plan, which was developed through listening to the needs of other government agencies, industry, academia and other stakeholders in the future of aviation. To reduce greenhouse emissions – carbon dioxide being the biggest contributor – you must reduce the amount of fuel burned. To be clear, we’re not talking here about coming up with a future airliner that flies faster than sound, or a smaller personal air taxi or package delivery aircraft of the type that will be part of Advanced Air Mobility. Airbus relies on its network of regional facilities for design and engineering activities. This work is assigned to design offices and engineering centres located in Europe and extending to North America, India, and China.
Our research in this area is characterized by strong connections with government organizations (NASA, FAA, DOD, DOE) and successful affiliations with industry (traditional aerospace companies as well as Google, Facebook and aerospace startups). It benefits from our local environment at Stanford and our global network of collaborators. Many of the design, modeling and computational methodologies we are developing for future aircraft are equally applicable to wind energy systems, underwater vehicles and, of course, space exploration. The preliminary design phase is where engineers go a step further into the design process to create a basic proof of concept. In this stage the engineers will calculate requirements that the airplane will have to conform with in order to fly, these can include Aerodynamics, Flight Mechanics, Structure stresses and stability.
No comments:
Post a Comment